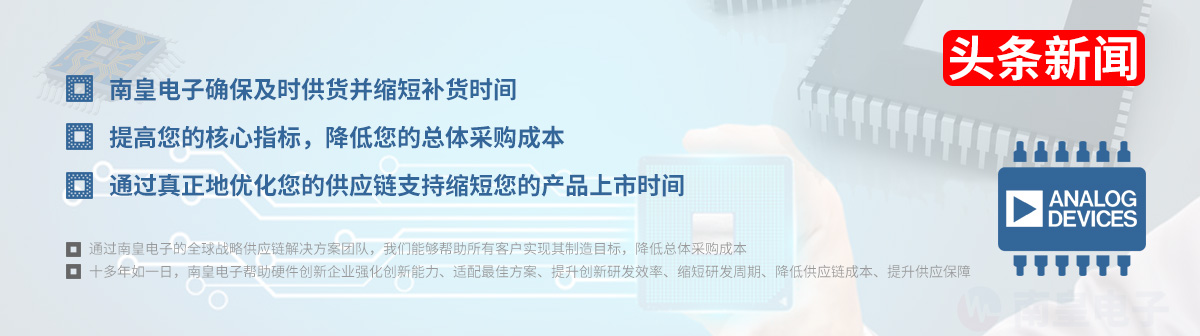
摘要
南皇电子专注于整合中国优质电子AD代理国内领先的现货资源,提供合理的行业价格、战略备货、快速交付控制AD芯片供应商,轻松满足您的需求AD芯片采购需求.(http://www.icbuyshop.com/)
AD公司提供基于单硅芯片的电池化成控制系统的综合解决方案 AD8452。每个电池的化学时间都可以通过精确的化学性能来优化。高效的能量回收特性可以显著节省大型电池制造的能耗。
简介
,锂离子(Li-Ion)制造是一个漫长的过程。准备必要的材料(电极、电解质、分离器等)。)在前三个阶段,并将其组装成电池。激活电池的最后阶段,使电池能够执行电气功能。这种激活过程称为电池化成。这种分级过程可以保证电池的一致性。存储容量低(低于5) A)锂离子电池广泛应用于笔记本电脑和手机等各种便携式设备。生产成本比生产效率更重要。同时,汽车电池的总容量要高得多,一般是数百个安培,通过数千个小电池单元或几个高容量电池实现。对于这类应用,电池的一致性更为重要,因此分级过程(提高电池的一致性)非常重要。同时,功率效率作为电池制造过程中化学成本的一部分,变得尤为重要。如果这些环保汽车使用的电池是通过浪费大量能源来生产的,那将是一个巨大的讽刺。
集成精密可用于模拟前端和降压-升压PWM控制器的单硅芯片来实现更高质量、更高效的电池化成/分级过程。该解决方案的精度优于0.02%,功效比高于90%。此外,在电池化成和分级过程中,其他电池制造过程可以回收释放的能量。许多现有系统将电池放电到阻性负载。一些客户将这种能量用作建筑供暖或直接将热空气排放到室外。尽管将电池放电到电阻负载是最简单的电池放电方式,但当大量电池需要充放电循环时,成本会迅速增加。我们提出的系统具有较高的单通道效率,但其真正的价值在于,该系统只需增加少量的复杂性就可以恢复电池放电时释放的能量。这种结构可以节省40%以上的能量。
简言之,基于AD8452单芯片解决方案使电池化成/分级过程具有以下特点:
u 降低电池成本
u 能量回收利用
u 高功效比
u 高测试精度
锂离子电池制造概述
图1显示了锂离子电池的制造过程。离线调节步骤中的电池化成和测试不仅是工艺瓶颈,而且对电池寿命、质量和成本有很大影响。
电池化成是对电池进行初始充放电操作的过程。在这个阶段,特殊的电化学固体电解质界面层将在电极上形成,主要是在阳极上(SEI)。该界面层对许多不同的因素非常敏感,对电池的性能有很大的影响。根据电池的化学性质,电池化成可能需要很多天。化成时使用0.1 C(C表示电池容量)电流是一种典型的做法,完成充放电周期需要20小时,占总电池成本的20%至30%。
图1.锂离子电池制造AD中国代理商过程。
1.可用于电气测试 C电流充电、0.5 C电流放电,但每个周期仍需三个小时左右。典型的测试序列需要执行多个周期。电池规格严格,电流和电压控制在额定温度范围内±0.02%以内。分级过程稳定了电池的电化学性能。根据现阶段记录的数据,具有类似电化学行为的电池将分为模块和/或电池组。这样,电动汽车的动力系统才能最大限度地一致。测量和控制精度将决定数据记录的质量,因此对整个电池电力系统的性能有不可忽视的影响。
汽车电池制造面临的另一个挑战是效率比。充电时效率也必须保持在较高水平,放电时应重新循环能源。这不仅有助于遵守环境保护政策,而且可以节省大型电池制造的成本。随着电动汽车应用的兴起,大型电池制造越来越受欢迎。
图2.围绕AD单通道系统由8452构建。
本单硅芯片解决方案将精确模拟前端和降压-升压PWM为了解决上述挑战,控制器集成在一个包装中。内膜匹配电阻有助于确保电流信号传感准确可靠。精心设计的模拟控制环路和PWM为了实现可能最优化的充放电操作,控制电路相互配合。实现的高性能可以降低系统定期校准和维护的工作强度,获得高功率转换和回收效率。这两者都有助于控制从材料到制造和维护的整个过程的成本。
电池化成和测试系统拓扑
设计工程师经常使用线性调节器来轻松满足便携式设备中电池化成和测试的精度要求,但会牺牲效率。对于大型电池,这种做法会导致热管理问题,效率会随着温度漂移而降低。
混合动力汽车中使用的大量电池必须完美匹配,这提出了更严格的精度要求,使开关拓扑成为一个有吸引力的选择。表1显示了各电池单元的功率容量和最终功能比较。
表1.对比线性和开关系统
图3.系统功效比测试结果。
降低电池成本
降低电池成本的困难在于它涉及到整个制造过程。本文描述的系统可以在不牺牲性能的情况下降低电池化成和测试系统的成本。更高的精度可以减少校准周期的时间和次数,进一步增加正常运行时间。此外,更高的开关频率简化了小体积电子元件的设计和使用,从而进一步降低了系统成本。该方案还可以并联使用通道输出更大的电流,操作非常简单。所有的控制操作都可以在模拟域中完成,无需开发复杂的算法,因此该方法也可以最大限度地降低软件开发成本。最后,能量回收功能,加上超高的系统效率,有利于大幅降低持续运营成本。
能量回收利用
与电池放电至阻负载的架构相比,基于AD8452构建的系统可以控制电池的电压和电流,并将这些能量推回公共总线,使其他电池组在充电循环中使用。每个电池通道都可能处于充电模式,从直流总线吸收能量式,将能量推回直流总线。最简单的系统包括单向系统AC/DC该电源只能将电流从交流市电拉入直流总线。这意味着系统必须保持准确的平衡,以确保来自AC/DC电源净电流始终为正。如果直流总线的电能超过充电通道消耗的电流,总线电压会增加,部分部件可能会损坏。
图4.具有电池芯间能量回收功能的电池测试系统。
双向AC-DC转换器通过将电能推回交流电网来解决上述问题。在这种情况下,所有通道都可以设置为充电模式,然后设置为放电模式,将电流推回电网。这需要更高的复杂性AC-DC转换器,但在系统配置上具有更大的灵活性,无需准确平衡充放电电流,即可保证电源电流为正。
图5.具有交流市电能回收功能的电池测试系统。
支持能量回收的效率
为了进一步展示能量回收的好处,请考虑两个3.2 V、15 A电池组。这些电池可以储存48左右wh的电量。假设充电效率为90%,系统必须向每个电池提供约53个.3 Wh的能量。在放电模式下,系统将减少48 Wh覆盖电阻中转换为热量的电能,或将其回收到总线。如果不回收,大概需要107 Wh给两个电池充电。但是,如果一个系统能以90%的效率回收能量,第一个电池的43.2 Wh现在可以给第二个电池充电了。如前所述,系统充电效率为90%,因此需要53.3 Wh,但其中43.2 Wh来自放电电池,所以我们只需要提供剩下的10个.1 Wh,也就是说,所需63.4 Wh.能量节省了40%。在实际生产环境中,不同的卷盘在整个生产过程中放置数百个电池,因此将每个卷盘设置为一组充放电模式不会增加总生产时间。
结论
开关电源可为现代可充电电池的制造提供高性能、高性价比的解决方案。AD8452可简化系统设计,系统精度优于0.02%,能效比高于90%,支持能量回收功能。与那些浪费放电能而不重复用于给其他电池充电的系统相比,可以节省40%以上的能源,有助于解决可充电电池制造的瓶颈,使混合动力汽车和电动汽车从生产过程中环保友好。
作者简介
Seraph Hu毕业于伯明翰城市大学,获得电子工程学士学位,在伦敦帝国理工学院获得集成电路设计硕士学位。他于2011年加入AD,专注一个专注于准确性的人DAC应用工程师。Seraph曾担任中国技术业务开发工程师,之后从事该地区的仪器仪表业务营销工作。他目前对电池测试非常感兴趣,但他也对探索未来的手机测试应用感兴趣。
- 数据采集 - 模数转换器(ADC)
- 电源管理IC - 稳压器 - DC DC 开关式控制器
- 线性器件 - 放大器 - 仪器、运算放大器、缓
- 线性 - 视频处理
- 评估板 - DC-DC 与 AC-DC(离线)SMPS
- 数据采集 - 数模转换器(DAC)
- 线性器件 - 放大器 - 仪器、运算放大器、缓
- 电源管理IC - 稳压器 - DC DC 开关稳压器
- 射频开关
- 电源管理IC - 稳压器 - DC DC 开关稳压器
- 电源管理IC - 监控器
- 电源管理IC - 稳压器 - DC DC 开关稳压器
- 帮助企业实现工业自动化转型升级,AD很认真
- ADALM2000实验:模数转换
- 隔离四端口以太网供电PSE 控制器 通过了 IEEE 802.3bt 一致性测试
- AD最新并购行动扩大了网络安全软件和服务能力
- AD积极采取行动,全力支持客户共同应对新冠肺炎疫情
- AD公司推出高度集成Rx/Tx转换器HMC8100和HMC8200
- 抢进77/79GHz雷达市场 AD/瑞萨连手进攻
- 移动医疗多产业融合推动中国市场突破100亿,AD全体征监测先进技术成为重要推动者
- AD收购宽带GaAs和GaN专业的放大器公司OneTree Microdevices
- 连接总线的产品生命周期(下)
- 连接总线的产品生命周期(上)
- AD公司的宽带RF合成器系统尺寸简单,设计功能全面,高达13.6 GHz的出色性能
